“Deposit the minimum amount of the highest quality weld metal with the largest gauge electrode or wire at the highest current in the shortest possible time.”
The Golden Rule maximises efficiency to save time – TIME is the single biggest cost in welding. This is particularly relevant in NZ as we are increasingly competing on a global basis against manufacturers and fabricators from countries with low labour costs. To compete we must improve our productivity/efficiency to save time and reduce labour costs.
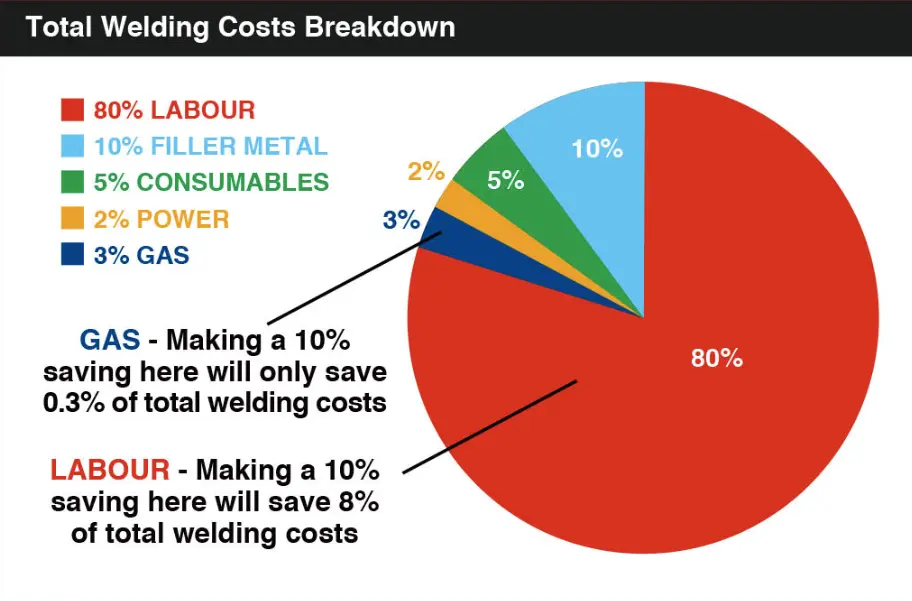
Shown above are standard approximations used in the industry. More often, the cost of the filler metal is well below 10% of total welding costs. Overheads such as plant, administration, are not included as they are usually not able to be influenced by decisions made in job costings.
So what does this mean? Look at the bigger picture to minimise your total welding costs.
As an example, a cheaper inferior MIG wire could translate into additional time spent in pre- and post-weld operations such as cutting, forming, surface and joint preparation, pre-heating, cleaning, tacking, grinding and painting.
So a minimal percentage saving in one area is well out-weighed by increased labour costs in efficiency-robbing activities elsewhere.
Another example, improve productivity in welding by increasing the duty cycle. This could be as simple as re-organising the shop floor or work process to improve efficiency and maximise arc time, or switch to a new technology welder which optimises and sets the welding parameters to maximise arc time and quality of welds.
Consider options in combination, e.g. switch to a water-cooled set up to enable welding at a higher current and use a metal cored wire which can be laid down faster.
Finally, always remember: time cannot be saved at the expense of meeting the required welding standards, weld procedures, or end product standards. Here’s where quality becomes vitally important.
- A quality MIG wire will provide accuracy in wire placement and consistency in the weld, significantly reducing rework.
- It can be more forgiving and produce a sound weld even under less than perfect conditions.
- The best quality wires are laid down faster, saving significant time.
- Using the best Mig wires should reduce wear and tear on consumable parts.
- A quality wire ensures consistent chemical composition, superior penetration and adhesion, which results in the best welds achievable.
*The Welding Institute (TWI) in the UK, one of the world’s foremost independent research and technology organisations.