Postweld heat treatment (PWHT) is generally carried out to relieve residual stresses, remove diffusible hydrogen, and temper hard transformation microstructures of the weld.
PWHT prevents brittle fractures and obtains the desired properties of the product. PWHT, however, can have some negative effects, such as stress relief cracking (SR cracking).
SR cracking can become a problem particularly in the PWHT of high tensile strength steel, heat-resistant low alloy steel and stainless steel weldments. Figure 1 shows a typical example of SR cracking that occurred in a 780-MPa high tensile strength steel weld that was heat treated at 600°C for 2 hours after welding. It is believed that this microscopic crack was initiated by the creep of the metal during relaxation of the residual stress at high temperatures particularly at the coarse grain area in the heat-affected zone (HAZ) at the toe of the weld. This is where the residual stresses are concentrated. And this crack propagates along the former austenite grain boundaries of the HAZ.
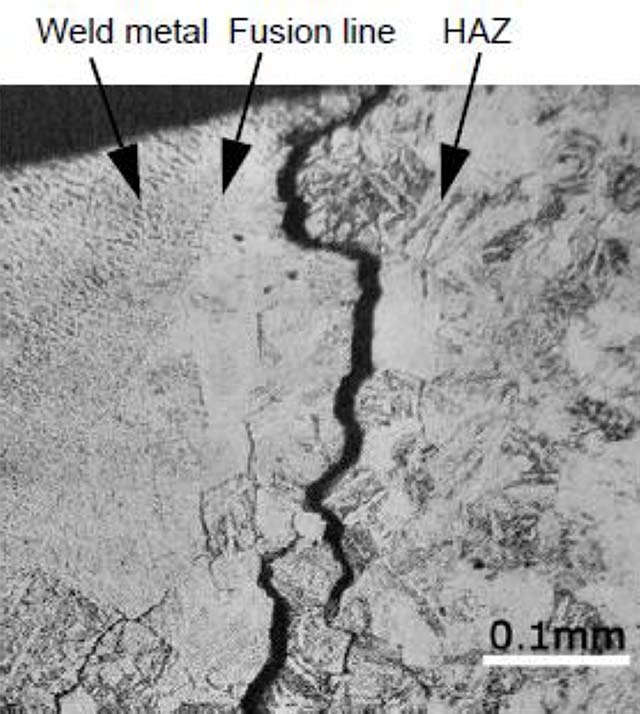
Figure 1: Typical SR cracks occurring in a 780-MPa high tensile strength steel weld (PWHT: 600°C × 2 h) [Ref.1]
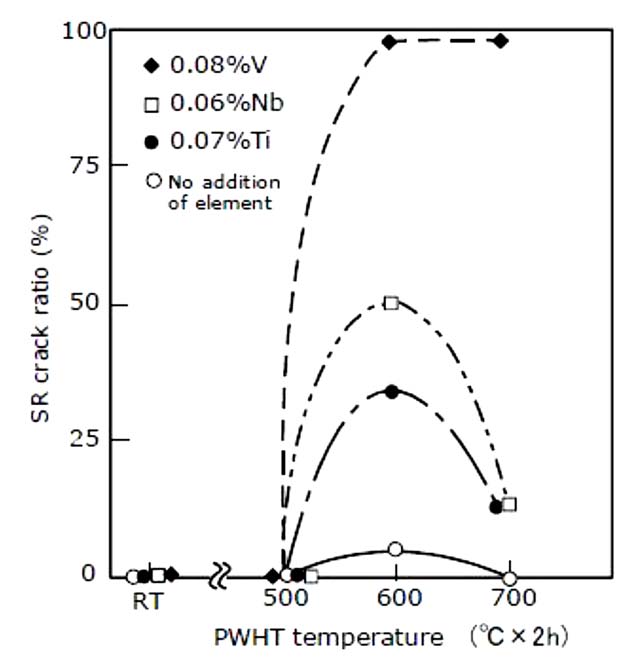
Figure 2: SR crack susceptibility of Cr-Mo steel (0.16%C, 0.30%Si, 0.60%Mn, 0.99%Cr, 0.46%Mo) as a function of PWHT temperature and additional alloying elements in groove restraint cracking test [Ref.2]
The SR-crack susceptibility of particular types of steel is governed by PWHT temperature and the alloying element.
Figure 2 shows how SR crack susceptibility is affected by particular alloying elements contained in the testing steels and PWHT temperature. It clearly shows that the crack susceptibility becomes highest at 600°C. This is believed to be caused by the alloying element’s carbide precipitation hardening of the crystal grains, thereby decreasing relatively the strength of the grain boundaries.
Ito and Nakanishi [Ref.1] suggest an SR cracking susceptibility index, PSR (%) = Cr + Cu + 2Mo + 10V +7Nb + 5Ti – 2, where the applicable ranges of alloying elements are 1.5%Cr max, 0.10-0.25%C, 1.0%Cu max, 2.0%Mo max, 0.15%V max, 0.15%Nb max, and 0.15%Ti max. It is believed that where PSR is larger than zero SR crack can occur.
TO AVOID SR CRACKING, THE FOLLOWING MEASURES MAY BE TAKEN:
- Select a less susceptible steel taking into account, for instance, the SR cracking susceptibility index (PSR).
- Refine the coarse grain HAZ at the toe of the weld by applying the temper bead technique.
- Dress the weld metal to smoothen the transition to the surface of the base metal, or remove the reinforcement of the weld metal to be flush against the surface of the base metal to minimize or remove the site of stress concentration.
- Avoid lapping a fillet weld onto a butt joint weld to prevent excessive residual stresses and stress concentration.
- Avoid joining components of excessively dissimilar thicknesses to prevent the high concentration of stress.
References
[1] H. Suzuki, et al. Welding Metallurgy, Sanpo Pub. Inc.[2] H. Ikawa, et al. Welding of Heat-Resistant Steel, Sanpo Pub. Inc.
Reproduced from Kobelco Welding, Japan.