THE LORCH COBOT UR10e
Quick to use and intuitive to operate for consistently high-quality, reproducible welding results with the key aim of increasing productivity.
WATCH: Cobot Move Linear Axis
Cost effective, smart welding to meet the demands of both today and the future. The LORCH Cobot Welding Package is available in New Zealand, call Welding Engineers on 09 634 1949 for more information.
Why automate with a LORCH Cobot System?
WATCH: LORCH Cobot Overview
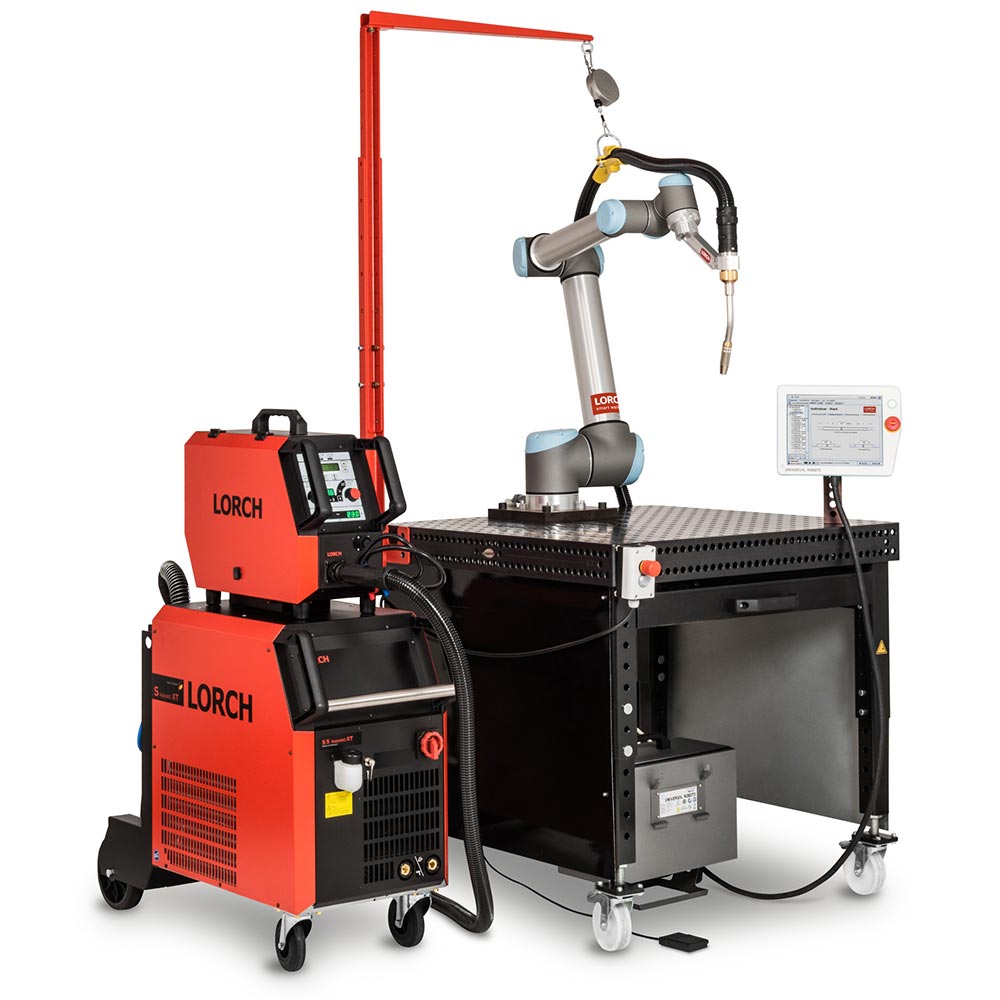
LORCH COBOTRONIC
What sets the Lorch Cobot Welding system apart from other Cobot solutions is the LORCH Cobotronic software designed specifically for combining the UR10e cobot with the LORCH welding machine.
- Easy set up, plug and weld
- Maximised user compatibility; choose Job, Assistant, or Individual mode
- Customisable Add-on Functions
- Future upgradability
- LORCH advanced welding technology
THE COBOT UR10e:
Made by Cobot market leader Universal Robots, the collaborative robot UR10e works side by side with humans safely and efficiently. The best robot technology in a small package allows easy automation in manufacturing.
- Flexible applications
- Fast to set up and deploy
- Portable
- Customizable
- Built-in safety features
- Simple programming
- Intuitive user interface
- Low-maintenance hardware
S ROBOMIG XT WELDING MACHINE
Hardware, designed and made in Germany by LORCH to exacting standards.
- ‘3 step to weld’ operating system
- Full Process – LORCH Speed Processes
- Tiptronic job memory
- Precision Feed system
- 4 wheel drive
Hardware Option
Cobot Move Linear Axis
More than 4.5m reach for long, large, and nesting operations.
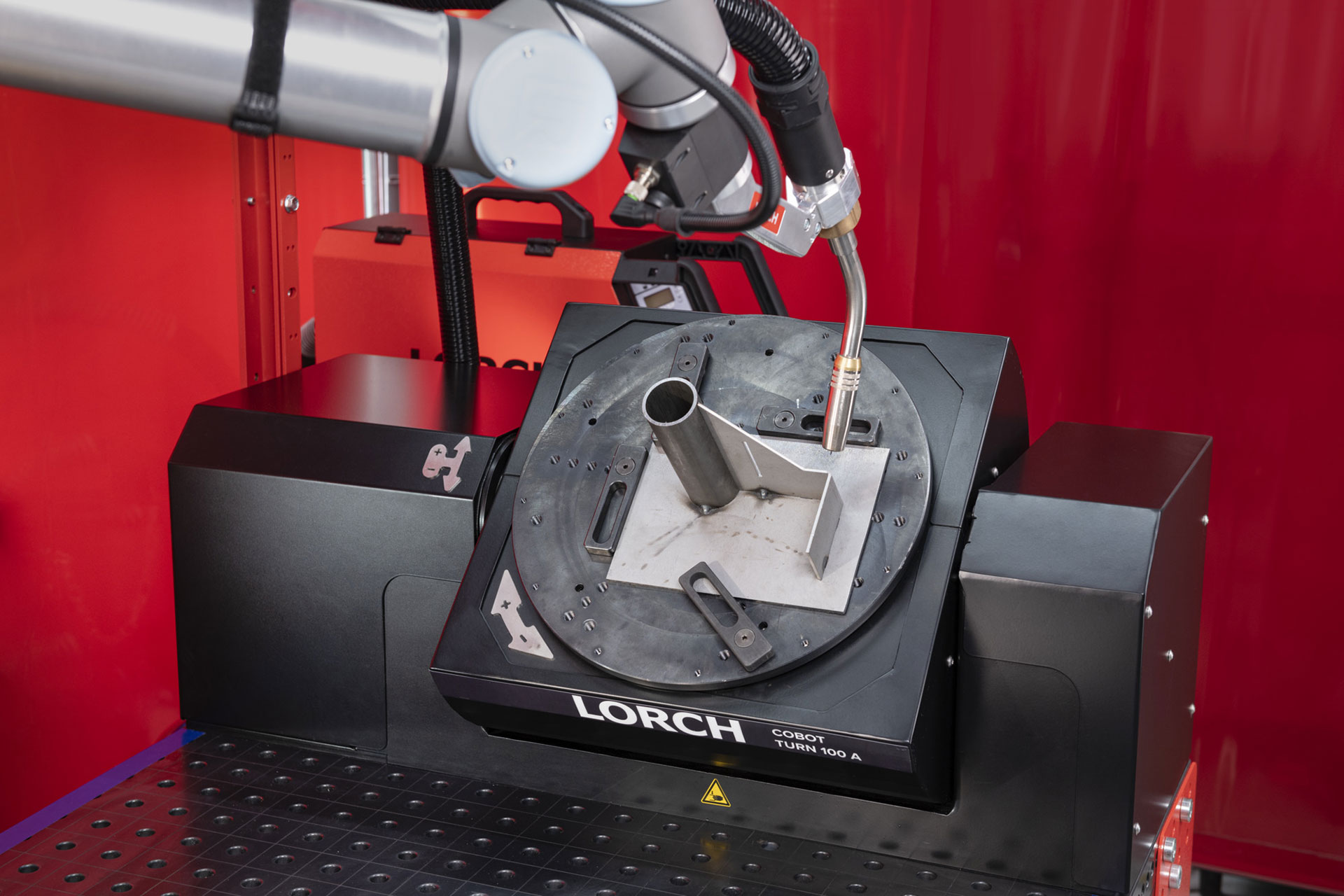
Hardware Option
Cobot Turn and Tilt
The two-axis positioner can be programmed instantly and intuitively on the common control panel of the Cobot. The Lorch Motion software enables the programming of the Cobot and the rotary tilting table to be coordinated. So the time consuming turning and re-clamping of the workpiece by hand is no longer necessary – valuable working time is saved and the welder’s workload is significantly reduced.
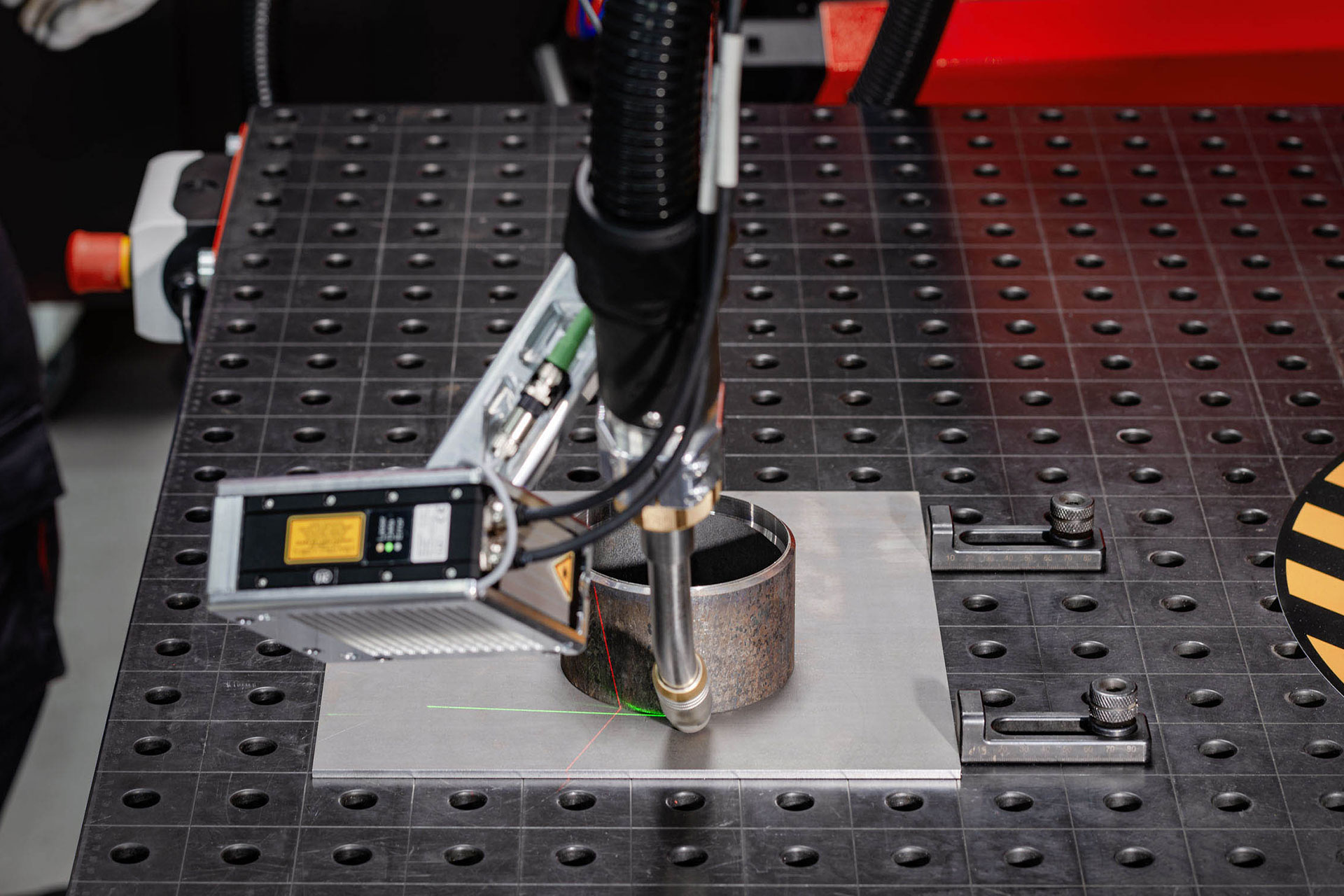
Hardware Option
Seam Pilot
SeamPilot utilizes a line laser on the welding torch bracket to make programming the Cobot and ensuring the perfect weld even easier. The operator simply has to show it a rough starting point. The line laser will then find the weld seam and follow it to the automatically detected end point, as in Seam Tracking. The laser line sensor predicts the course of the weld seam for the Cobot, permitting automatic welding of difficult courses in curves, waves, or circles, poor fit-out pieces, even variation in repeated jobs.
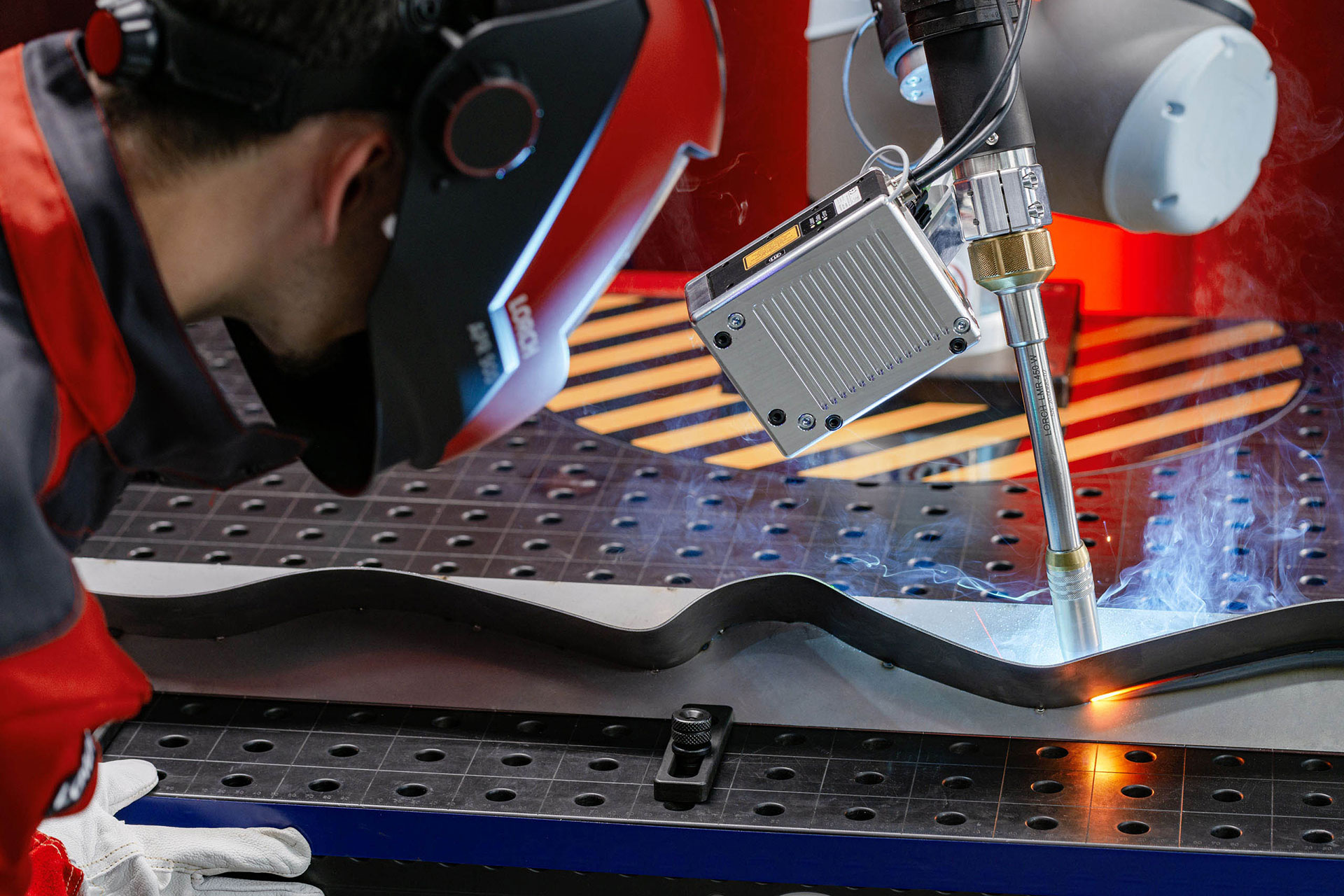
Hardware Option
Seam Tracking
Laser Seam Tracking weld correction automatically keeps the Cobot on the course of the weld seam regardless of deviations, distortion, or poor fit-up. Lorch sensor technology will detect the arc course during the weaving movement of the torch to ensure the torch stays at the centre of the seam and covers any gaps.
Plug & Weld:
The LORCH Cobotronic software designed specifically for combining the UR10e cobot with the LORCH welding machine for maximised user compatibility and ease of use.
Easy to Use
Time Efficient
Rapid ROI
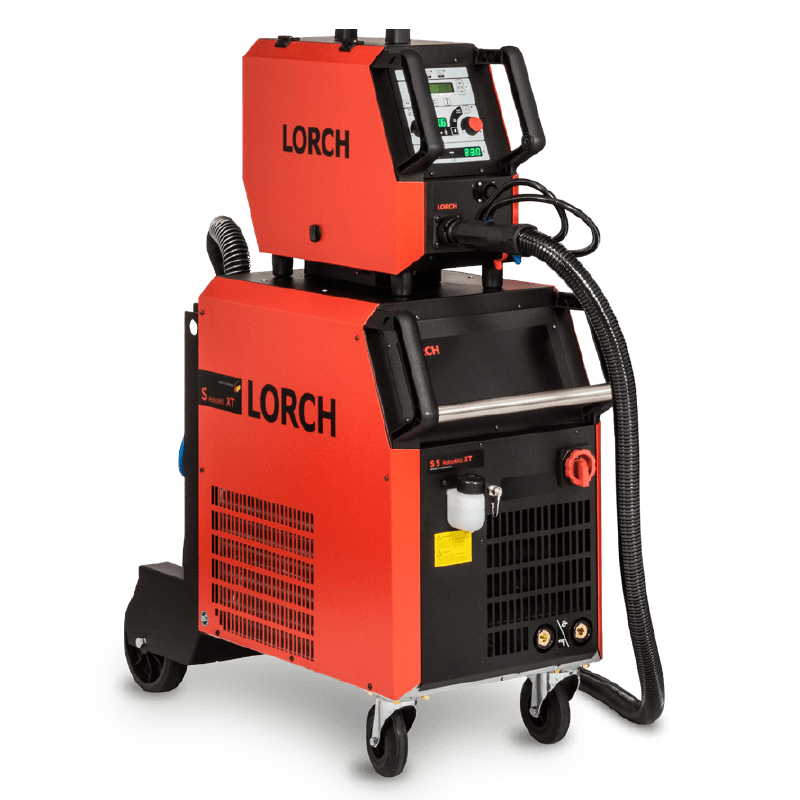
The Welding System
The LORCH Cobot Welding Package MIG-MAG Edition ships with the premium LORCH welding system S-RoboMIG XT plus high-end inverter technology, interface and precision feeder system. The high-performance power source of the LORCH Cobot Welding Package with its Full-Process equipment and lightning-fast control technology allows you to weld almost anything you want -with ultimate efficiency.
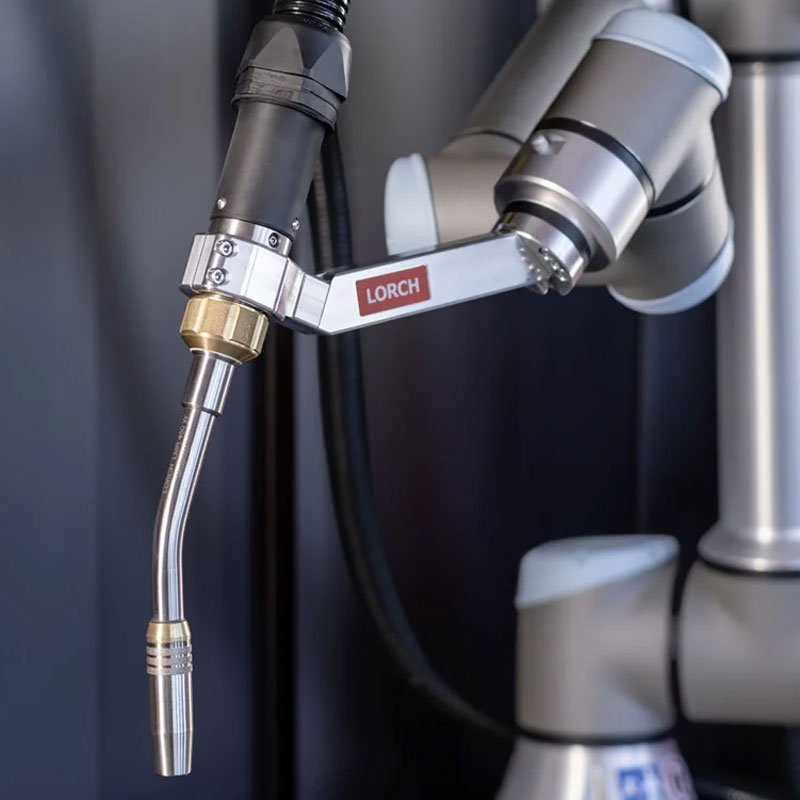
The Torch
The system is complemented by the torch LMR 450 W, which has been designed especially for MIG-MAG Cobot welding applications: The Cobot-optimised holder and the dual circuit cooling system for an extended service life of the wear parts provide for ideal welding performance and improved user safety.
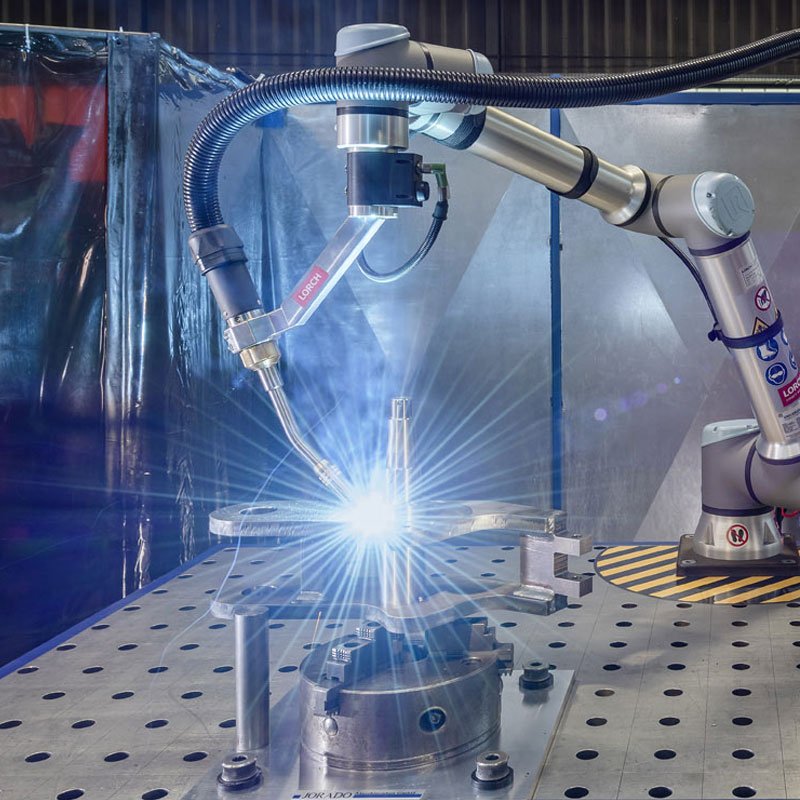
The Speed Processes
Better yet, all of our innovative Speed processes come standard as well. This guarantees the optimum welding process for each specific application. The TwinPulse XT, for instance, lets you produce appealing seams with a TIG look and a level of efficiency that cannot be beat.