Cold cracks are defined as cracks that occur at temperatures of 200-300°C or lower in carbon steel and low-alloy steel welds.
Cold cracks can occur in both butt welds and fillet welds; however, this article will focus on those occurring in fillet welds.
Typical cold cracks that can occur in fillet welds are illustrated in Figure 1.
Cold cracks come in several varieties: Toe cracks initiate at the weld toe with dimensional discontinuity where stresses are concentrated. Root cracks are caused by the concentrated stress at the notch of the corner of a fillet joint. A heel crack is an example of a root crack. Lamellar tears are subsurface terrace and step-like cracks in the base metal with a basic orientation parallel to the wrought surface. They are caused by tensile stresses in the through-thickness direction of the base metal weakened by the presence of small dispersed, planar shaped, nonmetallic inclusions parallel to the metal surface. Underbead cracks can be observed lying parallel to the fusion line in the heat-affected zone of a steel material that has high hardenability. Deformation cracks are caused by local plastic deformation concentrated at the toe or root of a multiple-pass weld. They can be toe cracks or root cracks. Finally, the HAZ and weld metal microcracks are microscopic cracks that can occur in a fillet weld under strong restraint.
HOW COLD CRACKS OCCUR AND HOW THEY CAN BE PREVENTED
Cold cracks, typically root cracks, can occur under particular metallurgical and mechanical conditions associated with
- the hardenability of welds,
- the amount of diffusible hydrogen in welds,
- the degree of restraint of weld joints, and
- the cooling rate of welds.
As these factors increase, the weld becomes more susceptible to root cracking.
Hardenability is determined by a combination of chemical composition and the cooling rate of the weld.
The amount of diffusible hydrogen varies depending on the type of welding process, the type of filler metal, contaminants such as moisture and oil in the groove surface, and the cooling rate of the weld. With a slower cooling rate, higher amounts of diffusible hydrogen can be discharged from the weld.
The degree of restraint varies depending on the type of welded structure: however, the thickness of the structural component is the predominant factor: the thicker the component, the higher the restraint.
The cooling rate varies depending on the welding heat input, plate thickness, and preheating temperature. In order to prevent root cracks, it is necessary to use a base metal with low-hardenability (good weldability), choose a low-hydrogen filler metal, and preheat the base metal to an appropriate temperature in consideration of the type of base metal and filler metal, and the thickness of the component to be welded. These measures are also somewhat common against other kinds of cold cracks listed in Figure 1. In addition, to prevent lamellar tears, the base metal must have sufficient through thickness ductility and its sulfur content must be low. The HAZ and weld metal micro-cracks are affected also by the content of nonmetallic inclusions.
In contrast, it is believed that deformation cracks (which can be root cracks or toe cracks) are not affected by diffusible hydrogen, temperature, and strength of the weld. To prevent the deformation of the components, weld joints should be sufficiently restrained.
REFERENCES
[1] The Japan Welding Engineering Society. MAG/MIG Welding Defects and Preventive Measures. Sanpo Publications Inc.
Courtesy of Kobelco Welding, Japan
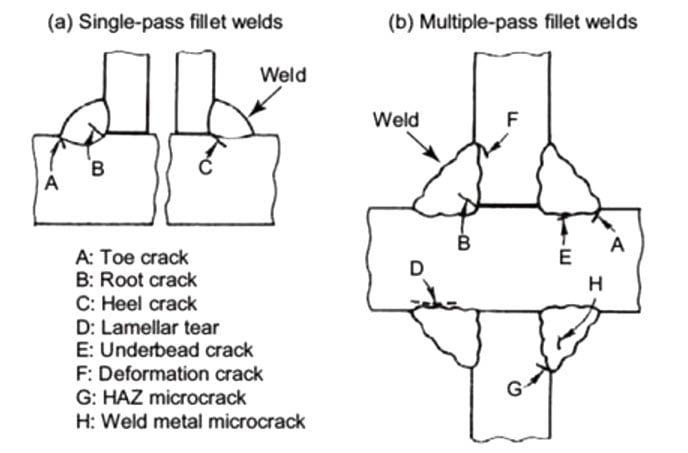
Figure 1: Typical cold cracks in fillet welds [1]