Advanced Control in Welding Application
Heat input is one of the most important factors affecting the quality of a weld due to its formative effect on the Heat Affected Zone (HAZ) and weld metal properties, particularly mechanical toughness, and development of potential flaws.
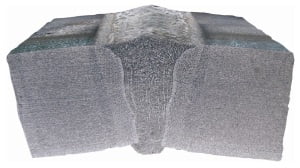
The size and severity of the HAZ are also affected by such factors as weld geometry, environmental conditions; but mostly depends on the amount of heat applied, the duration of exposure to heat, and the properties of the material and its filler metal. In terms of heat input, at its simplest, when a material is exposed to greater amounts of energy for longer periods the HAZ is larger.
Generally speaking, the higher the strength of the base material, the greater the need for precaution during welding. In most cases, problems arise when the heat input is too low or too high. Heat input that is too high, either through excessive voltage, excessive amperage, or slow travel speed, can slow your cooling rate, resulting in excessive grain growth. This results in changed mechanical properties, mainly a decrease in the material’s toughness. Too high a voltage can cause small amounts of alloy to be lost in the arc, directly reducing the effective mechanical properties of the welded joint.
Slow travel speed usually occurs when you attempt to fill a large joint with only a few weld passes. This raises the heat input drastically. The solidification rate of the weld pool occurs at a slower rate, promoting grain growth in the weld metal and HAZ. Similarly, the size of the HAZ decreases as the speed of the welding process increases.
So, controlling heat input more precisely can reduce the HAZ and weld flaws or deformation, and also helps avoid costly post weld corrective and clean up work.
Different welding equipment manufacturers have come up with a number of solutions for this; many of which rely on the development of digitally controlled synergic power sources and more precise control of the waveform. Software is only part of the solution, however; key breakthroughs come from deep understanding and manipulation of arc physics.
For instance, LORCH (leading German welding machine manufacturer) developed a unique Speed Arc process that manipulates and focusses the arc, which has the effect of significantly reducing heat input whilst allowing faster travel speeds, (see diagram).
The result is a better quality weld with smaller HAZ and deeper penetration, as can be seen in this weld cross-section.
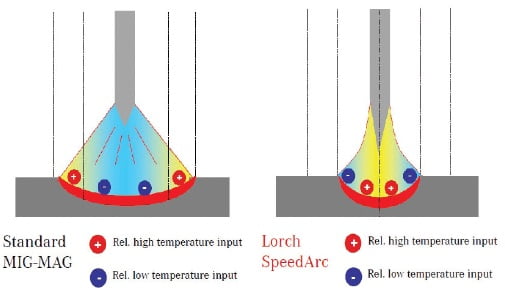
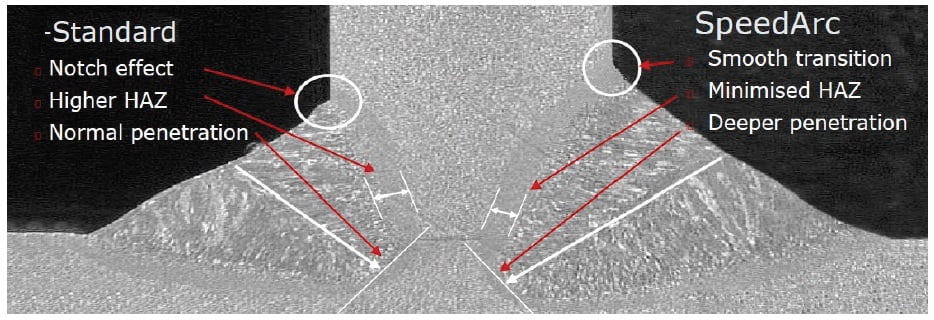
Another way to control heat input is to lock the parameters on your welding machine so the user must stay within the safe zone of voltage, amps, wire feed speed for the particular job, or simply lock in your weld procedure parameters. This is easily done with Lorch’s innovative NFC (Near Frequency Communication) cards on a LORCH MicorMIG machine.
In summary, controlling and reducing heat input means better welds, lower risk of weld faults, significant reductions in spatter, improved operator use and comfort, improved productivity.
Processes and capabilities which reduce heat input are an important feature to look for when choosing a synergic welding machine for both the benefits in weld quality and productivity gains.