“I’ve always used solid wire – works fine, does the job. Why change?” A typical comment we often hear, however… Change is definitely worth thinking about!
Depending on the application, using metal cored wire (MCW) can generate significant cost savings in conventional gas metal arc welding (GMAW) processes. It is ideal for robotic welding but is also suitable for so much more.
Metal cored gas-shielded wire combines the high deposition rates of a flux cored wire with the high efficiencies of a solid wire. Productivity improves with the increased deposition rates and higher travel speeds, combine this with the minimal spatter and lack of clean up required due to the slag free welds and your labour costs will reduce. Yes, the up-front cost of metal cored wires is higher but filler metals only make up at most 10% of a weld’s cost and gas around 3%. In almost all applications, labour accounts for 85% of the total cost so any significant productivity increase from switching to metal-cored wire will outweigh the increase in the filler metal cost.
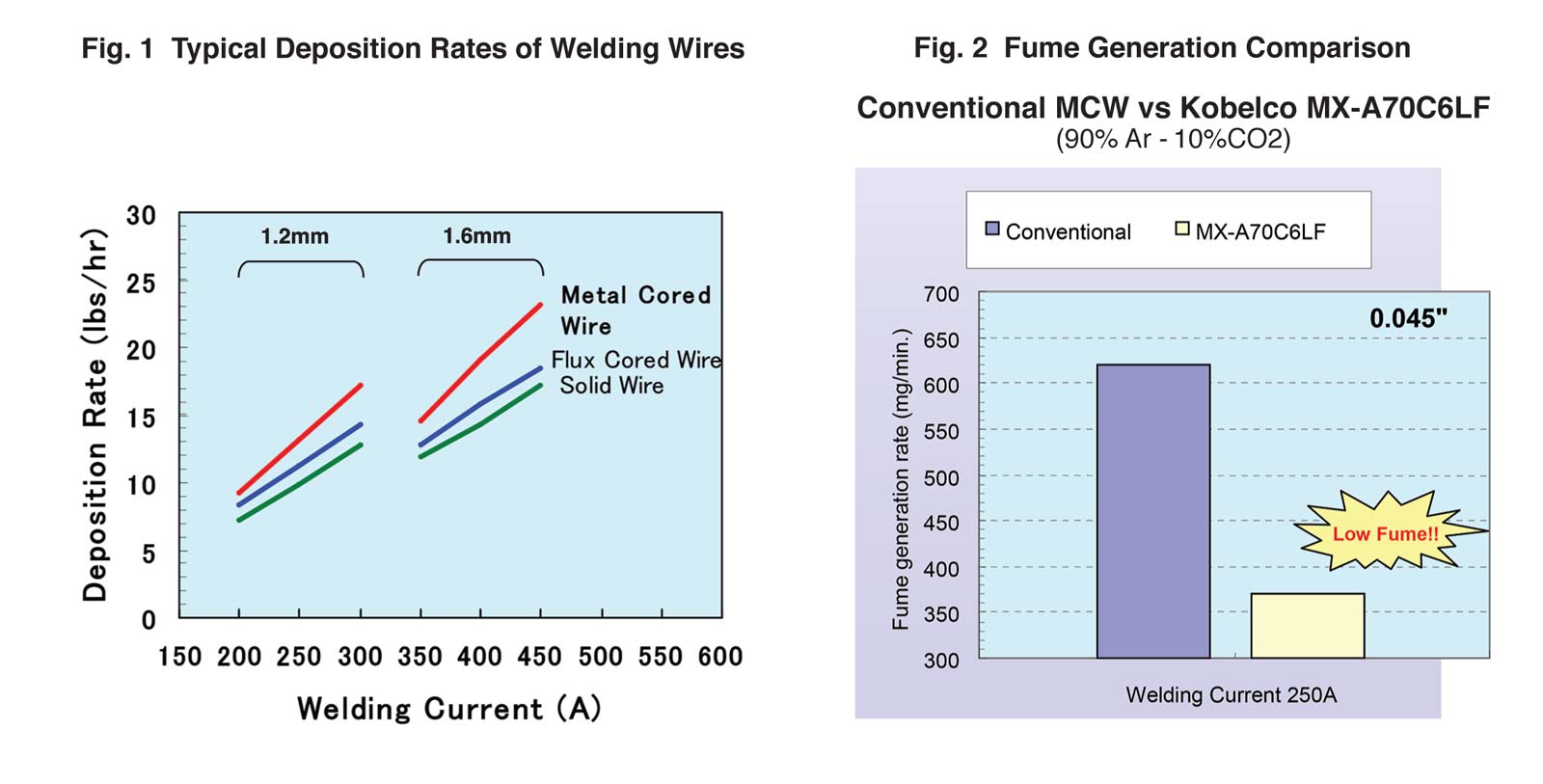
Concentrating the welding current through the outside tube of MCW results in a broader, bowl-shaped arc with finer droplets. This means MCWs fill imperfections and bridge gaps better, giving a quality weld with high structural integrity.
In addition, a quality metal-cored wire like KOB MX-A70C6LF, or NSSW’s SM-3A, runs much cleaner and smoother than solid wire, so not only extremely low spatter but less wear and tear on your tips, liners, drive rollers, etc, leading to savings in other consumable costs as well.
Welders usually prefer working with MCW as not only can they weld faster and smoother and easily produce great welds, their working environment is safer and healthier because of the much lower levels of fumes.
For an employer reducing risk in the workplace is a major focus of Health and Safety regulations and the NZ Dept. of Labour advises selecting welding consumables which create less fumes. In October 2014 in Victoria, Australia, a precedent was set for awarding compensation to a former welder who developed lung cancer.
The court accepted evidence from medical experts who said former welders were 44% more likely to develop lung cancer than the general population. Excellent ventilation is very important but real safety improvements can be made switching to MCW.
In summary, improved weld quality, improved productivity and improved working environment make very good reasons to investigate change.
As with other types of welding wires, metal cored wires are not all created equal, (see Fig. 2). There can be significant differences in quality and it pays to buy the best you can to gain the full benefits of using MCW.
If you would like to know more about the hows and whys of metal cored wire compared to solid and/or flux cored wires, check out our product range. For advice on whether changing to MCW would work for you, call us on 09 634 1949.